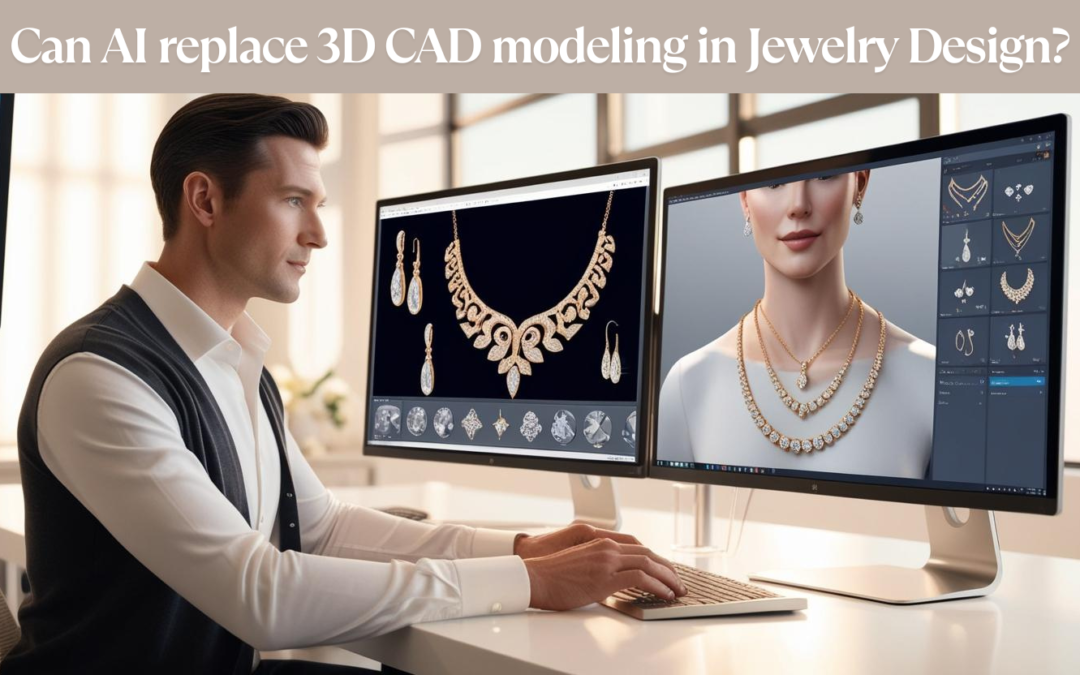
Can AI replace 3D CAD Modeling in Jewelry Design?
Our company has been focusing on 3D CAD design for custom jewelry for jewelers across the US and several other parts of the world. Having used traditional software tools like Rhino 3D and Z Brush, we can create 3D models using NURBS models and mesh modeling techniques. The rapid evolution of artificial intelligence (AI) has sparked conversations in almost every industry, and jewelry design is no exception. As AI-driven tools become increasingly sophisticated, many wonder if AI can fully replace 3D CAD modeling in jewelry design. While AI can automate several aspects of the design process, it needs to be seen if it can replace the human expertise in 3D cad modelling. In the below blog, let us explore what AI can achieve and cannot achieve in the foreseeable future.
Possible applications of AI in 3D Jewelry CAD design
1) Generative 3D CAD design: In this situation, the designer presents AI with a set of variables and the AI will propose multiple alternatives to the designer using those variables from which the designer can choose from. In jewelry design, this can be helpful to get possible alternative design options for a particular design style and stone type however the choise of the design alternative rests with the designer.
2) Automated 3D modelling: There are AI softwares that are capable of creating a 3D model using a sketch but these 3D models lack details that are very important to production. However for client presentation and design validation, these tools can be used to make 3D models to an extent.
3) AI design optimisation softwares: AI software can be used to optimise existing jewelry models and suggest better options to achieve different variables and these can be used once the model is ready.
Challenges faced by AI in 3D Jewelry CAD design
1) Creativity and jewelry knowledge: Jewelry design requires creativity and knowledge about the parameters of jewelry including manufacturing parameters covering a range of aspects. This is yet very difficult to achieve with AI.
2) Surface modelling: Jewelry design requires an artist to meticulously create surface models using their skill. They must design multiple surfaces, merge them seamlessly, and ensure each surface aligns with the design brief. This level of precision and artistic judgment is challenging for AI to achieve.
3) Complex Customisation: Clients seeking customised designs require a very specific kind of output whereas AI produces an output that could be similar but not exactly identical to the design brief. Human CAD designers can understand this brief and craft the models to perfection.
4) Complex surface design tools: There are complex surface design tools that require mesh modelling techniques and specific software tools such as ZBrush would be capable of doing the same. These kinds of output are rather difficult to create using AI and would require significant advancements to achieve such results.
Conclusion
Although AI can be a good tool in the hands of a jewelry cad designer to use and create options for a suitable cad design to be made, it is difficult for AI to completely take over jewelry cad design in the foreseeable future. AI could definitely assist designers by automating certain tasks such as generating design ideas and optimising models for production, it may not be able to replace the creative skills, precision required and engineering expertise of a human cad designer. The future could be a combination of AI-assisted tools and himan expertise to achieve the best possible results for jewelry designs.